ISO 23875 Cabin Air Quality Standard
Performance requirements for air quality control systems in operator enclosures for mining.
Scope: International Standards for Operator Cabins
What is ISO 23875 and Why Does It Matter?
ISO 23875 is an international standard published in February 2021 and updated in 2022, designed to unify the design, testing, operation, and maintenance of air quality control systems for operator enclosures, particularly in mining and heavy machinery industries. It aims to minimise exposure to harmful contaminants like respirable silica and carbon dioxide, protecting operator health, improving safety, and promoting productivity. By providing clear requirements and testing methods, ISO 23875 helps companies achieve their exposure reduction goals, ensuring compliance with global safety standards while enhancing operator comfort and morale.
Who Does the ISO 23875 Apply To?
ISO 23875 is particularly relevant to mining companies, equipment manufacturers, and health and safety professionals involved in the design, operation, and maintenance of air quality control systems for operator enclosures. It also applies to regulatory authorities and industry consultants responsible for ensuring compliance with safety standards. Organizations seeking to protect workers, minimize exposure to harmful contaminants, and align with global safety benchmarks are strongly encouraged to adopt this standard. Compliance not only supports health and safety goals but also enhances operational efficiency and competitiveness in the global market.
ISO 23875:2021/Amd 1:2022 Requirements
- Monitor Carbon Dioxide (CO₂) Levels:
-
- Sustained CO₂ levels must not exceed ambient CO₂ + 400 ppm.
-
- Respirable Particulate Matter – Decay Test:
-
- Maximum particulate concentration before and after the decay test: ≤ 25 μg/m³.
- Decay time for respirable particulate matter: ≤ 120 seconds.
-
- Cabin Pressurisation During Operation:
-
- Minimum sustained pressure: ≥ 20 Pa.
- Maximum sustained pressure: ≤ 200 Pa.
-
- Filter System:
-
- External air and recirculation filters must meet ISO 29463 classification standards.
- Use prefilters or powered precleaners to extend filter life and improve efficiency.
-
Source: ISO 23875:2021/Amd 1:2022, Section 4 – Requirements and Section 5 – Performance Testing
- Operator Enclosure:
-
- The enclosure must be sealed to prevent contaminant ingress caused by vibration or leaks.
- Safety structures like ROPS and FOPS must NOT be modified without manufacturer approval.
- Use materials that resist particulate accumulation and are easy to clean.
-
- Air Quality Control System:
-
- External air must pass through high-efficiency filters before entering the enclosure.
- The system must include a pressurisation mechanism.
- Filters must comply with ISO 29463 for efficiency and classification.
-
- Ventilation and Airflow:
-
- Design airflow to minimise operator exposure to contaminants:
- Supply air through the top half of the enclosure.
- Return air through the bottom half to remove particulates efficiently.
-
- Noise and Visibility:
-
- The system must not produce hazardous noise levels.
- Added components must not impede operator visibility. If unavoidable, provide mitigation measures like cameras or mirrors.
-
Source: ISO 23875:2021/Amd 1:2022, Section 4.2 – Engineering Design
- Pressure Monitoring:
-
- Device accuracy: ±10 Pa.
- Resolution: 5 Pa minimum.
-
- Carbon Dioxide Monitoring:
-
- Use NDIR sensors with:
- Range: 0 to 5000 ppm.
- Accuracy: ±3%.
- Response time: ≤ 20 seconds.
- Altitude and temperature compensation.
-
- Monitor Alarm Threshold:
-
- First alarm: Visual and audible alert at ambient + 400 ppm CO₂.
- Second alarm: Repeated visual and audible alert at 2,500 ppm CO₂.
-
Source: ISO 23875:2021/Amd 1:2022, Section 4.3 – Monitoring Devices
- Scheduled Maintenance
-
- Set a maintenance schedule with planned intervals to prevent system failures.
- Document inspections, replacements, and service history for traceability.
-
- Accessible Design
-
- Design systems for quick, tool-free access to filters and components.
- Arrange components for efficient servicing without unnecessary dismantling.
-
- Filter Inspection and Replacement
-
- Inspect filters for wear or damage and replace as needed.
- Ensure proper sealing during installation to maintain performance.
- Record filter details, including batch number, production date, and efficiency classification.
-
- Clear Filter Labeling
-
- Use ISO-compliant labels showing manufacturer, lot number, efficiency, and airflow.
- Include machine-readable labels (e.g., QR codes) for quick information retrieval.
-
Source: ISO 23875:2021/Amd 1:2022, Section 4 – Requirements and Section 6 – Operation and maintenance instructions
Exceed ISO 23875 with BreatheSafe
ISO 23875 |
BreatheSafe |
Performance Requirements |
|
CO₂ Monitoring: Maintain levels ≤ ambient CO₂ + 400 ppm. Particulate Matter Decay: ≤ 25 μg/m³ after ≤ 120 seconds. Cabin Pressurisation: 20–200 Pa during operation. Filter Requirements: ISO 29463 compliant with prefilters/powered precleaners for extended life and efficiency. |
✅ HEPA Filters: ✅ High Capacity Pressurisation: |
Engineering Design |
|
Operator Enclosure: Seal to prevent leaks or vibration ingress; use easy-to-clean, particulate-resistant materials. Do not modify ROPS/FOPS without manufacturer approval. Air Quality Control: Use high-efficiency filters with pressurisation and filter all external air before entry. Ventilation: Design airflow to reduce contamination by supplying air from the top and returning it through the bottom. Noise & Visibility: Minimise noise; ensure visibility or mitigate with cameras/mirrors if obstructed. |
|
Monitoring and Alarm |
|
Pressure Monitoring: Accuracy ±10 Pa, resolution ≤5 Pa. Carbon Dioxide Monitoring: NDIR sensors with 0–5000 ppm range, ±3% accuracy, ≤20-second response, and altitude/temperature compensation. Alarm Thresholds:
|
|
Routine Maintenance |
|
Scheduled Maintenance: Establish routine intervals to prevent failures; document inspections, replacements, and service history for traceability. Accessible Design: Ensure tool-free access to filters and components for efficient servicing with minimal dismantling. Filter Inspection & Replacement: Check for wear or damage, ensure proper sealing, and log batch numbers, production dates, and efficiency classifications. Clear Filter Labeling: Use ISO-compliant labels with manufacturer details, lot numbers, efficiency ratings, and airflow direction; include QR codes for quick data access. |
|
What You Need For ISO 23875
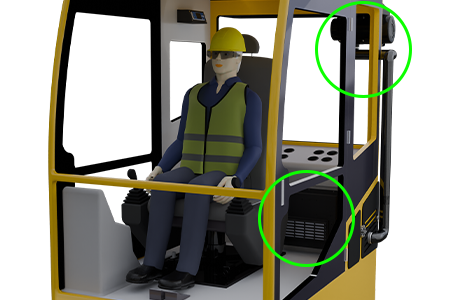
Closed-Circuit HEPA Filtration
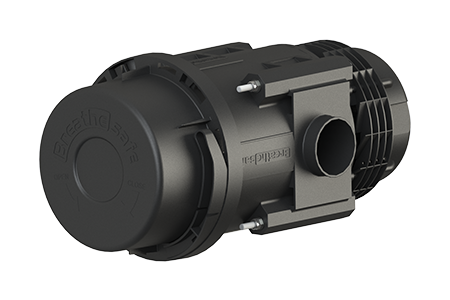
High-Efficiency Filters
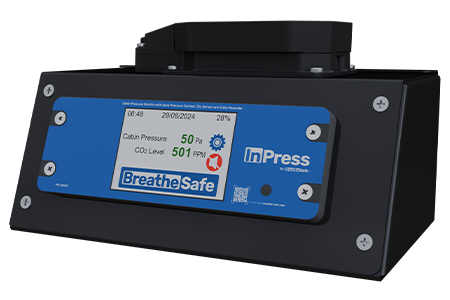
Controller with CO₂ Sensor
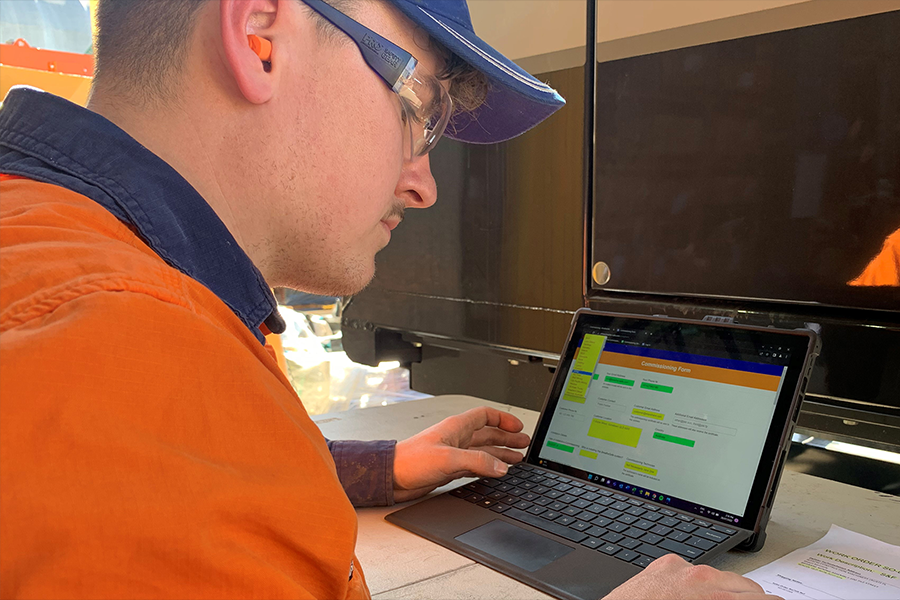
System Auditing Registry
Media
Need an ISO 23875 Solution?
Speak with our team to ensure your systems meet and exceed ISO 23875 requirements in any environment.