In high-risk industrial environments such as mining, tunnelling, construction, and heavy machinery...
RPME is the best practice to stop respirable dust
RPME is the Best Practice to Stop Respirable Dust
June 06, 2021
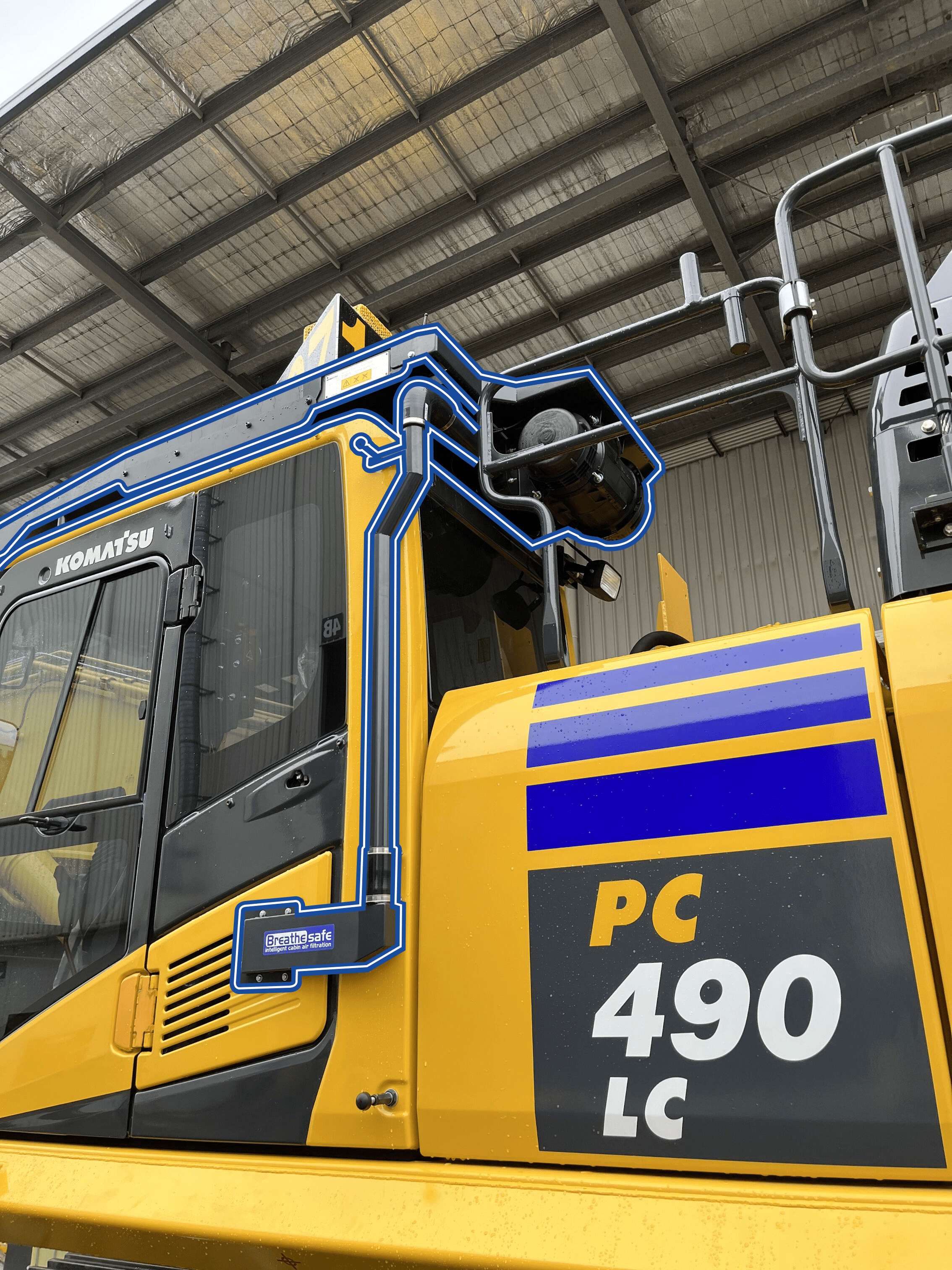
BreatheSafe Air Pressuriser System installed on a Komatsu PC490LC-11
RPME Respirable Particulate Mitigation Ecosystem:
A system, or group of interacting elements designed to protect the operator’s breathing zone environment
Bolting a pressuriser to a cabin without proper seals will not function well at all. Leaks in the cab will allow dust contamination to enter. The filters will be loaded by dust much sooner due to the higher volume (positive pressure) of air delivered to maintain a higher pre-set pressure (Positive pressure leakage).
The issues:
- A cabin by itself can no longer be assumed to resolve issues with respirable dust
- An environmental cabin serves as the primary method of dust control for operators for both surface and underground
- An environmental cabin/enclosure simply means that it can maintain a pre-set pressure level, for example: 20 pascals minimum.
- The effectiveness of the cab is maintained when the operator remains inside with doors and windows closed
- The HVAC must be well designed to cope with fresh air pressurisation (Hot/humid outside air)
BreatheSafe can assist with systems upgrades (Condensing) in very hot situations
- The fresh air pressuriser is filtered with HEPA media to separate respirable dust
- HEPA return air filters are fitted to control respirable dust inside the cabin (Particulate matter in shoes and clothes)
- The benefit is HVAC internal components remain dust free; reducing unscheduled repairs and/or machine standing down due to failure.
Provisos:
– Auditing and testing the entire system
The cabin requires proper sealing to maintain positive pressure: Door and window seals must be replaced as soon as damage and/or leaks are detected.
WORK SMARTLY AND SAFELY
The best practice is to have a multitude of systems in place: Pre-cleaner and a fresh air HEPA pressuriser system matched to an environmentally sealed structure and which is pressurised to a controlled pre-set level. Procedures of sealing all gaps and making sure that window and door seals are in good working order are also required. The cabin must be kept clean always, with doors and windows remaining closed at all times.
Utilising a computer-controlled display system and citing an international standard such as EN15695 (Hazardous substances) is necessary as it states that the ideal pressure level is between 20 to 50 pascals for ONE person cabin. EN15695 imposes an absolute minimum: 20 pascals with a pressure display (Operator awareness) or 50 pascals without a pressure display.
Breathe-Safe system EN15695-4 system consists of:
- Environmental cabin/enclosure (Tight against airborne particulate)
- Pre-cleaner to expel coarse particulate (Extends the life of HEPA media)
- HEPA filter forced ventilation (Fresh air pressuriser)
- HEPA return air filter
- Display (Operator awareness)
- Remote Monitoring (Site management/maintenance)
- Activated carbon media for Gaseous particulate
- Fresh air volume minimum is 30m³/h for one person cabin to avoid CO2 build up
Exposure to respirable dust impacts worker health in the short and long term as well as on productivity for both man and machine. The other issue that needs to be understood is that fine dust does cause HVAC system contamination (HVAC internal restriction) over time and leads to unscheduled maintenance situations and other related issues such as underperforming climate control. The BreatheSafe ecosystem is effective at limiting respirable dust exposure to almost zero levels for the operator. Remote monitoring can be used for data management and systems review. It can also be used to provide training for operators where a window or door have been left open.
The conclusion is the sum of elements to protect the operator/s must remain effective over the entire lifecycle of the cabin/enclosure.
Related Articles
Comparing Cabin Filtration Systems: What is the BEST?
BreatheSafe at the Underground Operators Conference
As the Underground Operators Conference approaches, we caught up with Kelvin Wright, BreatheSafe’s...
Holiday Closure Dates
Thank you to all our customers, suppliers, friends and family for a wonderful year! During the...